International helmet certification options
What do bees, gel pads and modelling clay have to do with biking? Quite simple: they can save your neck when a stunt goes wrong. Modern MTB protectors are full of amazing tech. We explain why some concepts offer better protection, why lighter isn’t always better, and how the specialists at MET Bluegrass test their products.
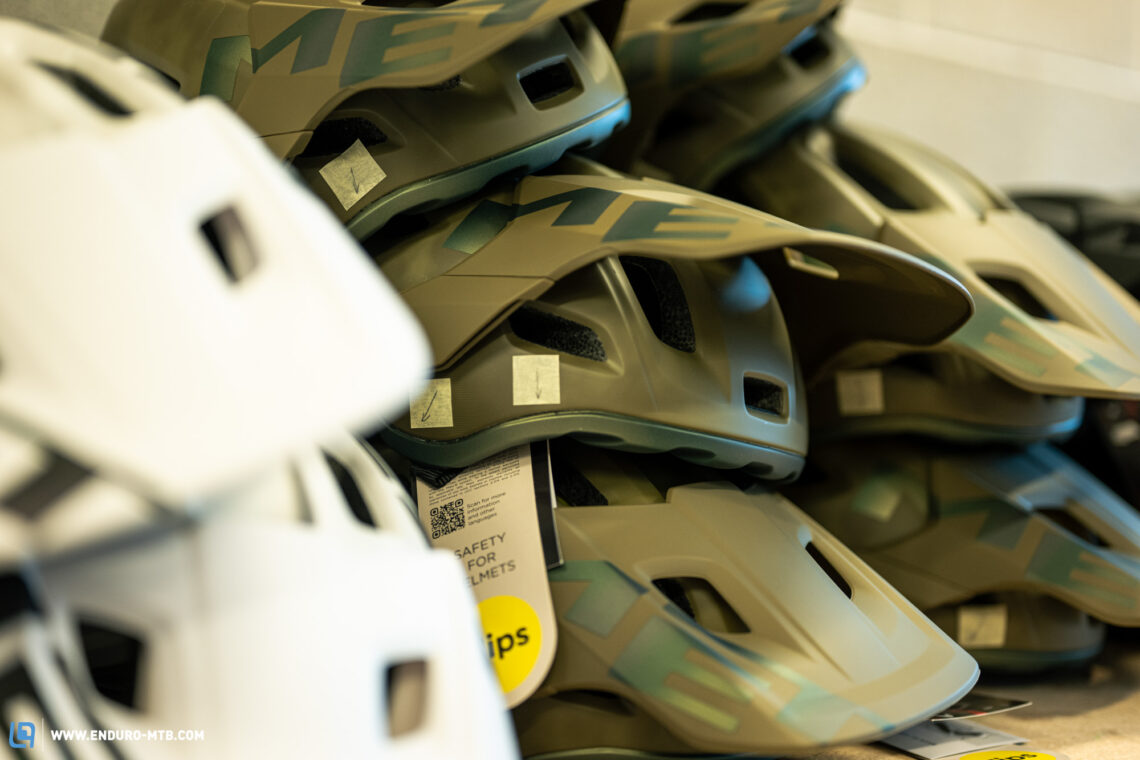
Helmet and knee pads on and you’ve got the best protection possible, right? Hardly! Like our bikes themselves, bike protectors have become high-tech devices. The aim is clear: our safety gear must be comfortable, stylish, light, and offer adequate protection, of course. If you’re happy with your old and smelly 2 kg downhill helmet and think it’s as good as any, you clearly haven’t tried on one of the lightweight and well-ventilated full-face models of the latest generation, complying with the same safety classification and allowing you to remove the chin guard for the climbs. And it’s not just the helmets that are high-tech. Knee and elbow pads as well as chest and back protectors have long said goodbye to the era of scratchy, hard plastic, now offering better protection, breathability, odour resistance, and conforming to your body. You’ve lost your faith? Keep calm, you’re at the right place. Read our safety bible to learn what to look for when buying protective gear and what ultimately matters when things go pear-shaped.
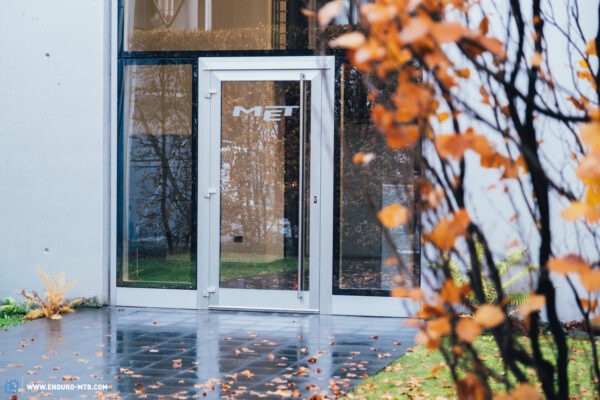
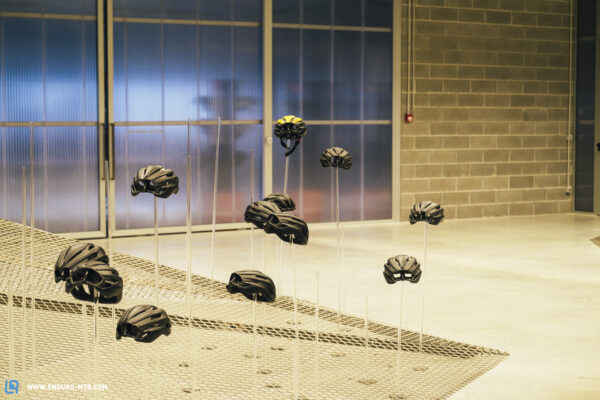
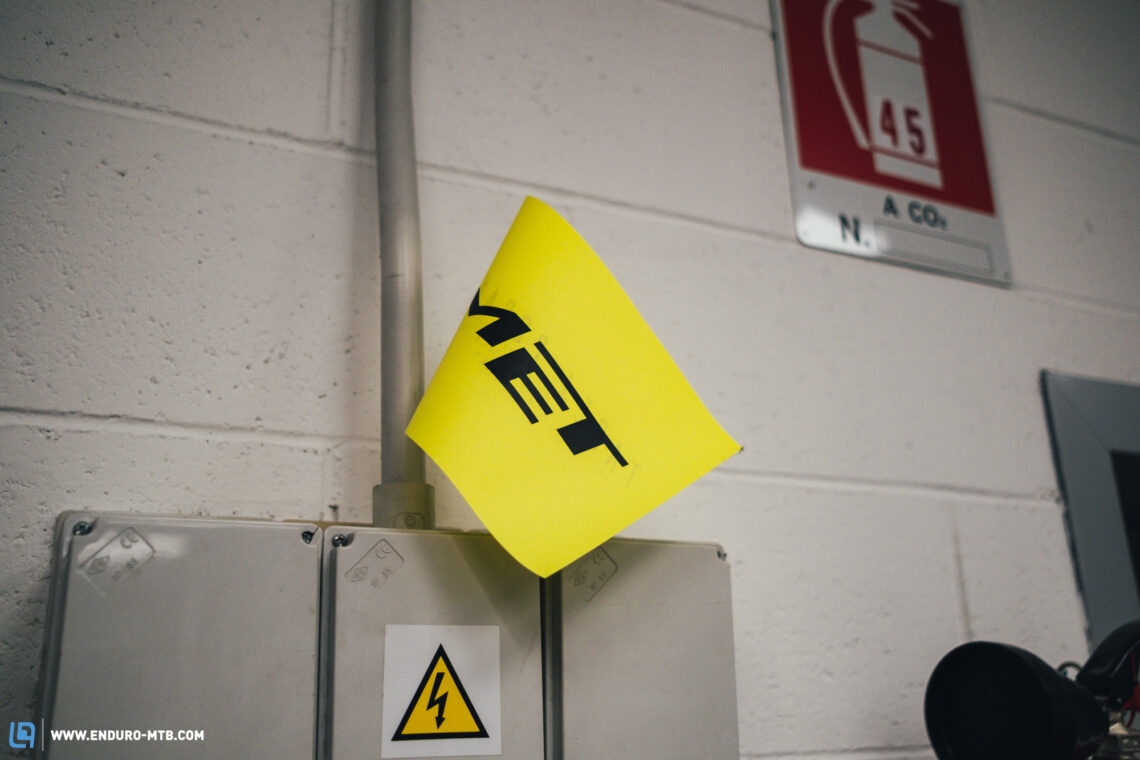
Protective gear of the future
There are different methods and technologies available to keep our heads and bodies in one piece when we crash. We visited the protection specialists at MET in their Italian headquarters and picked their brains to find out more. That said, not all roads lead to… Italy. We set out to find an answer to the question of how to best protect yourself when you’re out riding your bike. Like the Seamless Lite D3O back protector from MET Bluegrass, other products from other brands can perform just as well and have also been awarded the coveted Design & Innovation Award. However, it’s easier to understand all the different technologies once we’ve taken an in-depth look at one particular instance. So, come along with us to Italy to get a better idea of the entire world of protective gear.
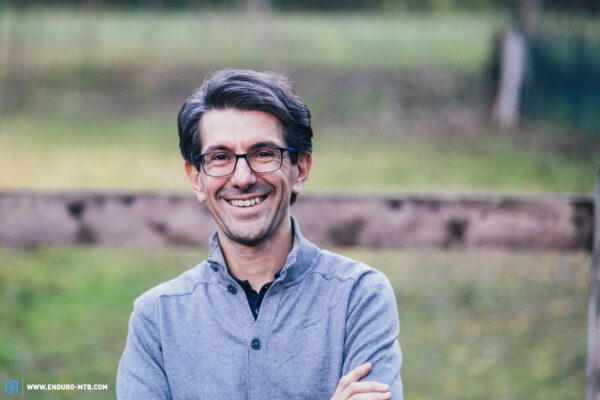
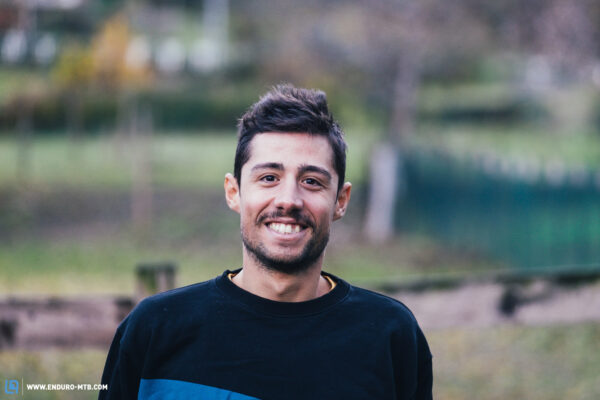
Of bees, gel pads, and modelling clay
The technologies that you’ll find in modern helmets and protectors are based on different principles. Some of them have been copied from the natural world while others seem to have taken their inspiration from children’s playgrounds. What they have in common is that they work, and that they comply with the relevant standards. Different manufacturers share some of these technologies for certain applications and thereby underline the strengths that the various protection concepts can offer. And depending on your specific demands and use cases, they can all work. We’re not out to pit the different brands against each other, though, but rather to explain how the technologies work and give you our experiences with different products. Moreover, the fit and comfort is always going to be a very subjective matter.
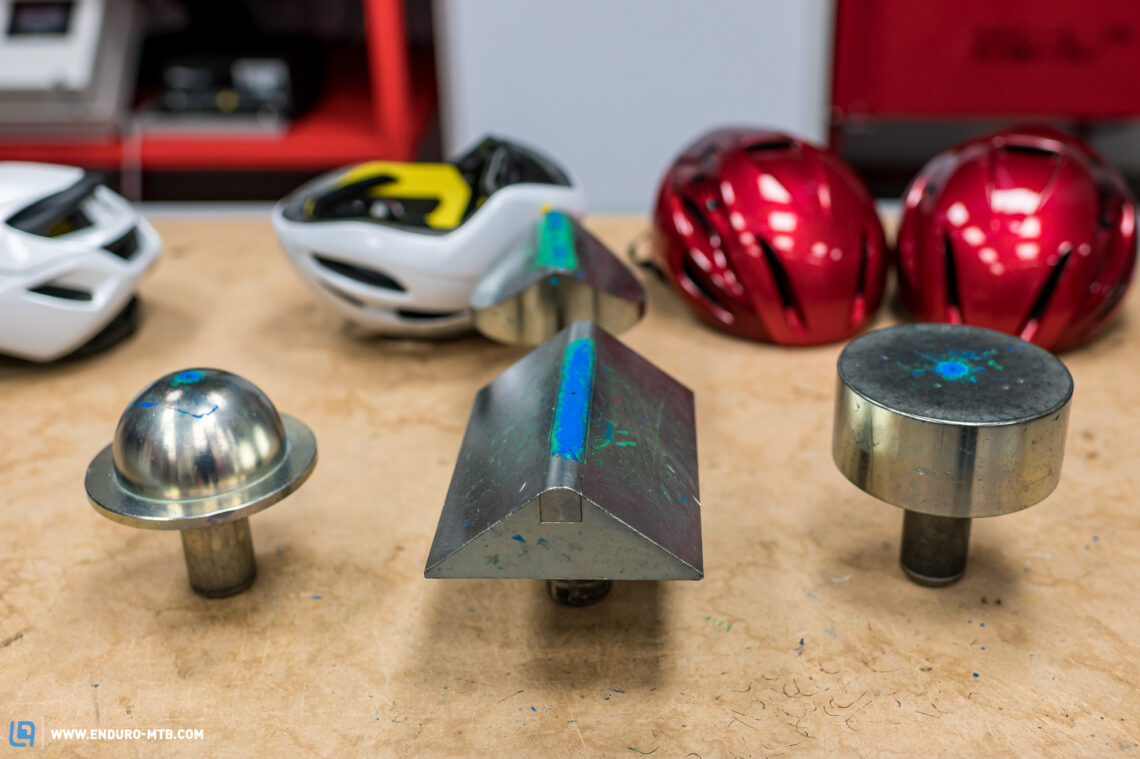
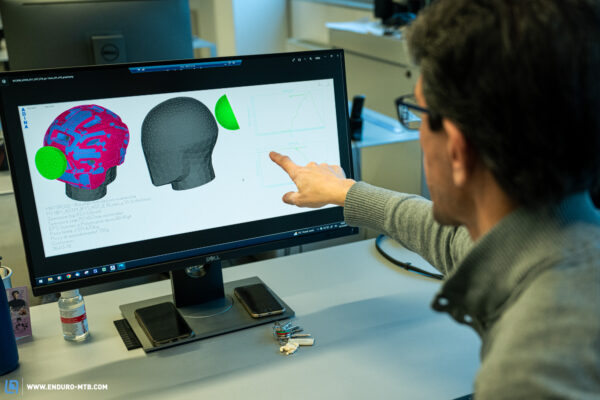
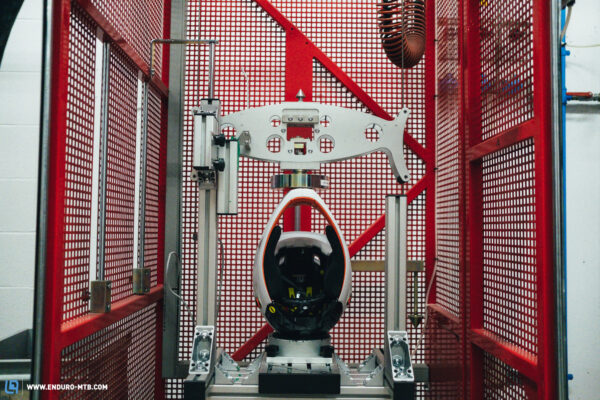
Certificates and approvals – What to look for when buying a helmet
There are five important helmet certifications available. Why so many? Three of them are needed to comply with the requirements of different regions: Europe, USA, and Australia and New Zealand. There’s standard that’s been developed specifically for s-pedelecs – ebikes that offer support up to a top speed of 45 km/h – and then there’s the most exciting standard for hardcore enduro and downhill use that includes the chin guard in the test procedure. Note: helmets that meet the latter-mentioned ASTM standard are compulsory at most big races like the Enduro World Series. So, you should check whether your helmet complies with the required standards beforehand. For better ventilation on the climbs, you’ll even find a wide selection of good looking convertibles with a removable chin guard that meet this standard, like the MET Parachute.
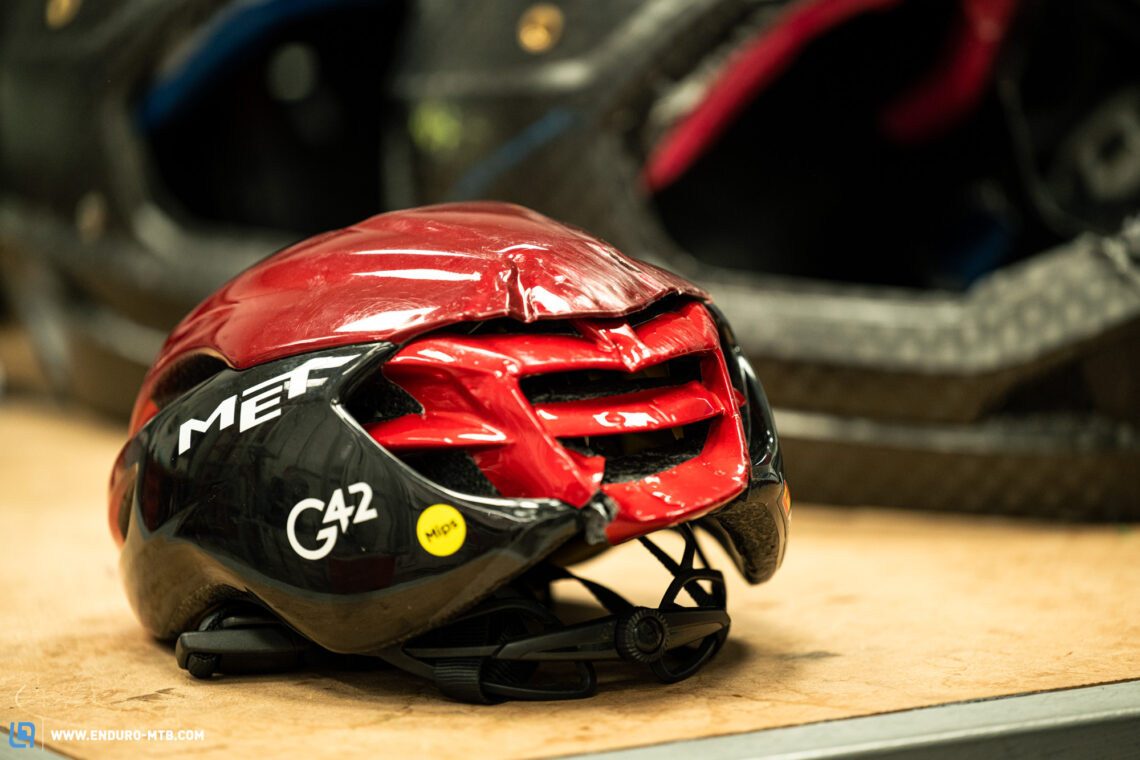
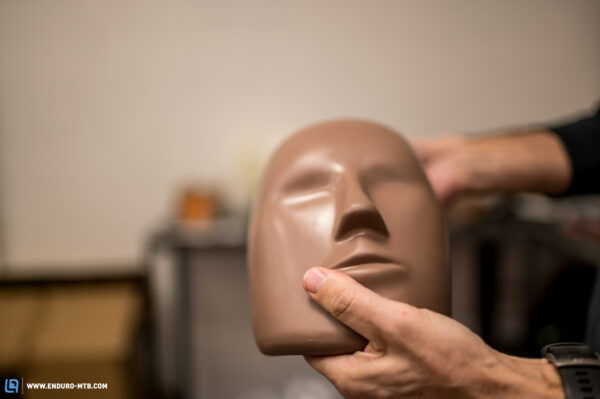
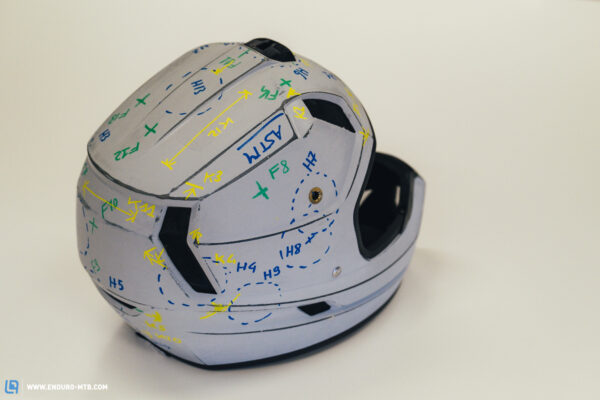
Without the CE stamp of approval according to the DIN EN 1078 testing standard, helmets aren’t allowed on the European market. However, the test standards aren’t the newest and they don’t get updated often enough to keep up with the technological advancements of manufacturers, so you can rest assured that most brand name helmets easily exceed the testing requirements, absorbing impacts better than required. The problem is that the standards are so low that you can get a helmet for under € 20 that still meets the requirements. So, with more expensive – and therefore hopefully better – helmets, it becomes difficult to distinguish the level of protection they offer and understand the value of the different protection technologies. All you know for sure is that they meet the basic standards. To make things easier for you, we’ve compiled a list of the most common testing procedures and the relevant technologies, giving short explanations of each.
International helmet certification options
Small disclaimer: the specifics of the standards can get very technical and dry. You might want to get yourself a drink for this – or a lexicon ;).
DIN EN 1078 / CE standard: required in Europe and many other regions around the world
To meet the DIN EN 1078 standard, helmets must be subjected to two crash simulation impacts, each directed at a different location on the helmet. A steel head gets placed inside the helmet and then dropped once onto a flat anvil and once onto a curbstone anvil. With the flat anvil, the weighted helmet gets dropped from 1.5 m, and it gets dropped onto the curbstone anvil from 1.07 m. In doing so, the force exerted on the head is not allowed to exceed 250 g equivalent to 9.81 N/kg. That’s 250 times the earth’s gravitational force. The measurement is taken by a triaxial accelerometer inside the steel head. These tests get conducted with the helmet being cold, hot, at room temperature, and in a rain simulator.
CPSC standard: USA
To comply with CPSC standards, each helmet must undergo four crash impact simulations, each directed at a different location on the helmet. A steel head gets placed inside the helmet and then dropped once onto a flat anvil, once onto a curbstone anvil, and once onto a spherical anvil. The weighted helmet gets dropped onto the flat anvil from a height of 2 m, and from a height of 1.2 m onto the other two anvils. The maximum force exerted on the head is not permitted to exceed 300 g. That’s 300 times the earth’s gravitational force. The measurement is taken by a triaxial accelerometer inside the steel head. These tests get conducted with the helmet being cold, hot, at room temperature, and after being dunked into water. The tests are harder on the material than they are in the EU, but the maximum permissible force experienced by the head is higher, too.
AS/NZS 2063:2008 standard: Australia and New Zealand
To comply with Australian and New Zealand standards, each helmet must undergo four crash impact simulations, each directed at a different location on the helmet. A steel head gets placed inside the helmet and dropped onto a flat anvil from a height of 1 m. Apart from that, a curbstone anvil gets dropped onto the stationary helmet. That corresponds to the opposite crash scenario. In other words, a stationary cyclist who gets hit by a moving object. In the standard scenario, the maximum force exerted on the head isn’t allowed to exceed 250 g. In the opposite simulation (force transfer test), the maximum value can’t exceed 500 N. These tests get conducted with the helmet being cold, hot, at room temperature, and after being dunked into water.
NTA 8776 (not compulsory): Dutch testing procedure simulating higher speeds, predominantly for s-pedelecs.
To meet the NTA 8776 standards, helmets must be subjected to two crash simulation impacts, targeting two different locations. A steel head gets placed inside the helmet and then dropped once onto a flat anvil and once onto a curbstone anvil. With the flat anvil, the weighted helmet gets dropped from 2.15 m, and it gets dropped onto the curbstone anvil from 1.5 m. The maximum force exerted on the head is not permitted to exceed 250 g. That’s 250 times the earth’s gravitational force. The measurement is taken by a triaxial accelerometer inside the steel head. These tests get conducted with the helmet being cold, hot, at room temperature, and in a rain simulator.
→ That corresponds to the maximum force allowed in the CE tests, though with a higher force being exerted on the helmet. Therefore, the helmet must be more robust.
ASTM 1952-15/2032-15 (not compulsory): Certification for the chin guard and shell
To comply with ASTM standards, each helmet must undergo four crash impact simulations, each targeting different locations. The ASTM certification only applies to full-face helmets since it also tests the chin guard. For the tests, a steel head gets placed inside the helmet and then dropped once onto a flat anvil, once onto a curbstone anvil, and once onto a spherical anvil. The weighted helmet gets dropped onto the flat anvil from a height of 2 m, and from a height of 1.7 m onto the curbstone and spherical anvils. The maximum force exerted on the head is not permitted to exceed 300 g. That’s 300 times the earth’s gravitational force. Moreover, a flat anvil gets dropped onto the chin guard from 40 cm. The maximum deformation allowed is 60 mm. These tests get conducted with the helmet being cold, hot, at room temperature, and in a rain simulator.
Manufacturers like MET try to keep the maximum deformation of the chin guard below the permissible 60 mm. According to MET, the sweet spot is around 30 mm. That way the chin guard isn’t so stiff that all the force gets transferred to the rider’s head, allowing it to deform enough to absorb some of the impact. Yet it’s stiff enough not to deform too much and thereby protect your face. The next time you’re wearing your full-face helmet, check how much distance there is between the chin guard and your mouth – you’ll probably find that it’s closer than 60 mm.
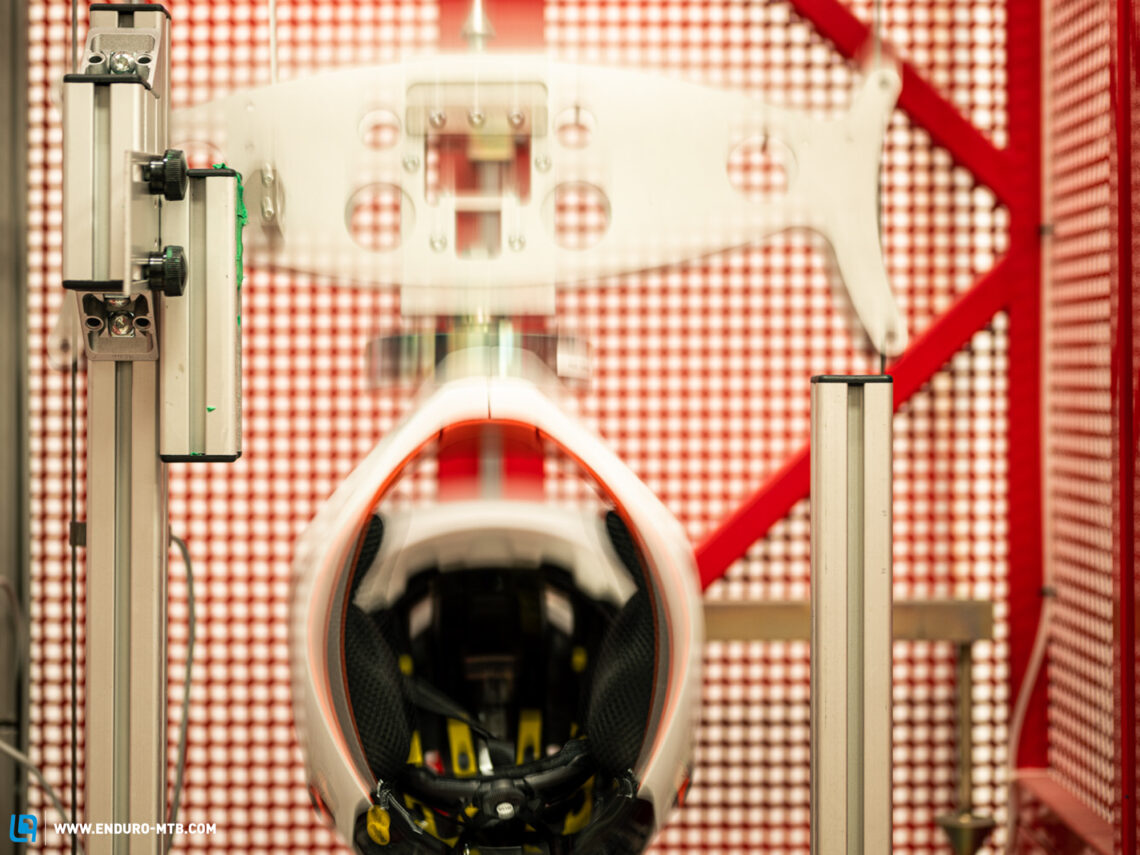
Helmet conditioning (compulsory for all tests)
The helmets must get conditioned to certain temperatures before all tests, with the hot condition specified to be +50°C, cold is -20 °C, and room temperature is 20 °C. During the tests, the helmets must remain effective within this 70 °C temperature range, not becoming too stiff and brittle when they’re cold or overly soft when they’re hot. As such, the helmet is guaranteed to protect your noggin just as effectively whether you’re riding in the depths of winter or if you’ve had it lying in the blistering sun. Speaking of which, the helmets also get artificially aged before the tests, subjected to 48 hours of 125 W ultraviolet light. This is to guarantee that the EPS foam of the shell doesn’t get damaged by strong direct sunlight, remaining flexible and shock absorbent. A brittle helmet won’t provide adequate protection.
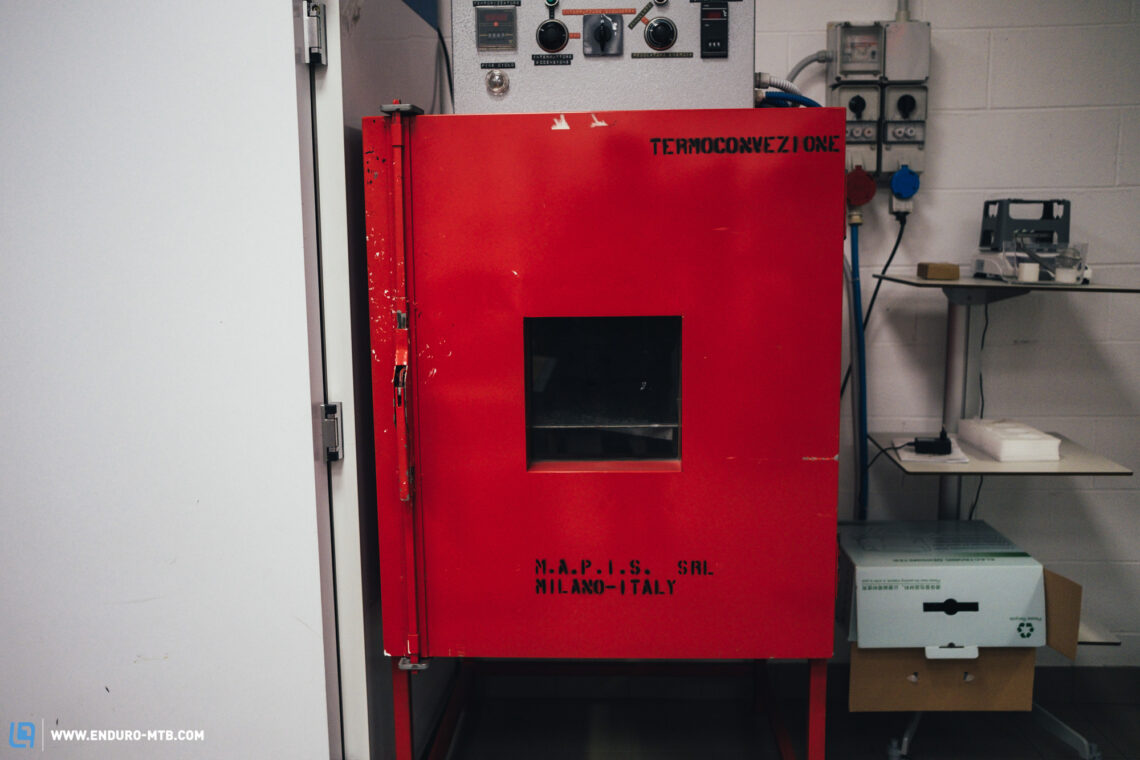
Additional helmet safety systems
Most manufacturers have gone beyond fulfilling the legal requirements, equipping their helmets with additional safety systems and features. They all have their own ways of making helmets safer. However, there is no standardised testing method for any of these systems, most of which are designed to reduce rotational forces. As such, there’s no easy way of comparing them, leaving it up to you to decide which system you’ve got more faith in. Some manufacturers rely on an in-house rotation protection system, while others resort to specific technologies like MIPS, which you can find in many helmets.
EPS foam – The basis of almost all helmets
Almost all helmets are based on a shell made of EPS foam. This shock absorbing material is reminiscent of very dense polystyrene. In case of a crash, the tiny air bubbles trapped inside the foam act as shock absorbers. The braces of the helmet can break in the process, but that further mitigates the impact. You should definitely replace your helmet after a crash. Even if it doesn’t look broken, the foam might not be as effective at absorbing a second impact and offer adequate protection for your head.
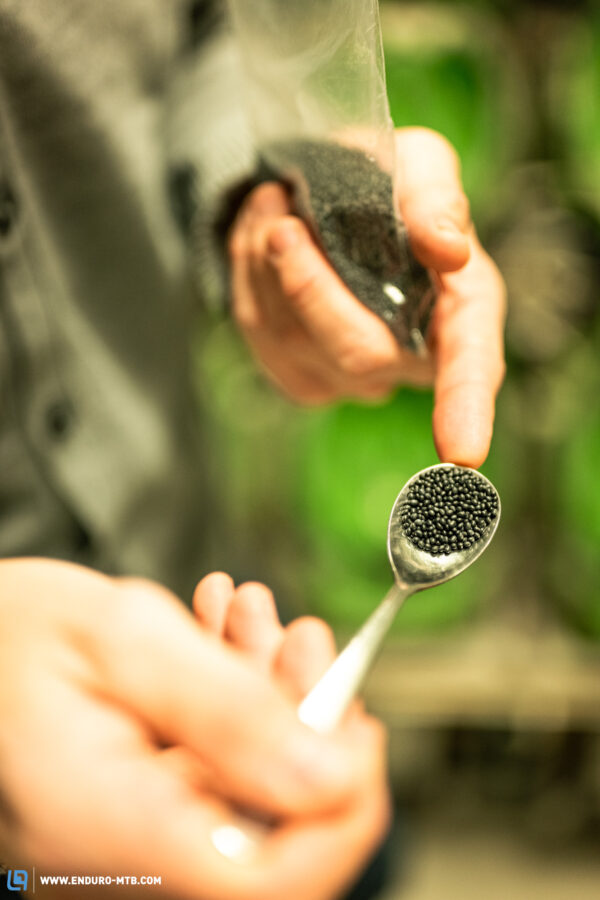
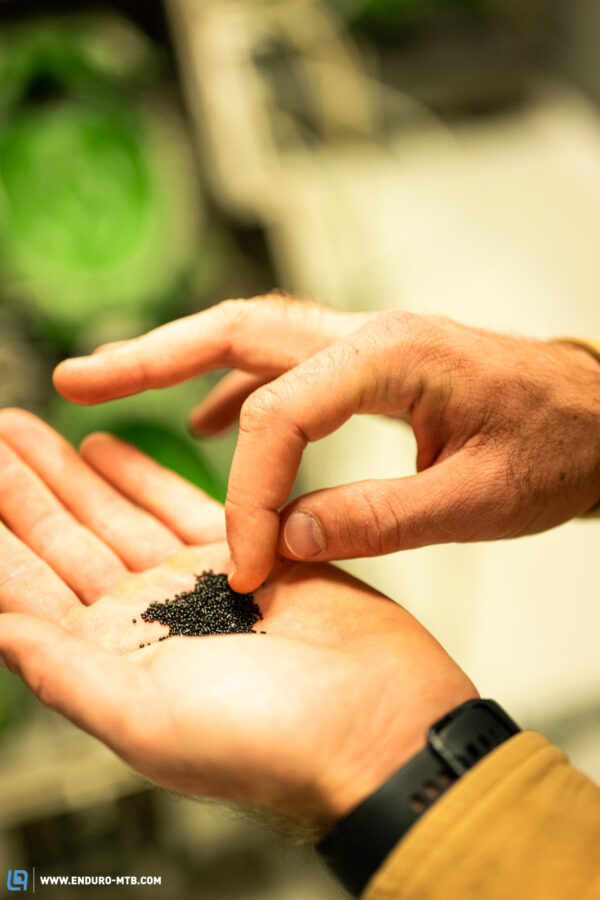
MIPS – How does the classic system work?
Since almost no crash happens at a perfectly right angle, MIPS have taken it upon themselves to reduce rotational forces acting on the head. Put simply, the helmet should twist upon impact, not your head. The Multidirectional Impact Protection System (MIPS) is usually quite easy to recognise thanks to the yellow sticker on the outer shell of the helmet, and you can usually spot the yellow membrane on the inside of the shell, too. This low-friction membrane is attached to the inside of the helmet, forming a kind of second layer that can move independently of the outer shell. Besides the distinct yellow membrane, there are other MIPS systems that are integrated into the pads or such that the helmet shell itself is split into two pieces. By mitigating rotational forces, the MIPS system is said to reduce the risk of concussions and neck injuries. Several well-known helmet manufacturers like MET Bluegrass rely on the patented system for their helmets.
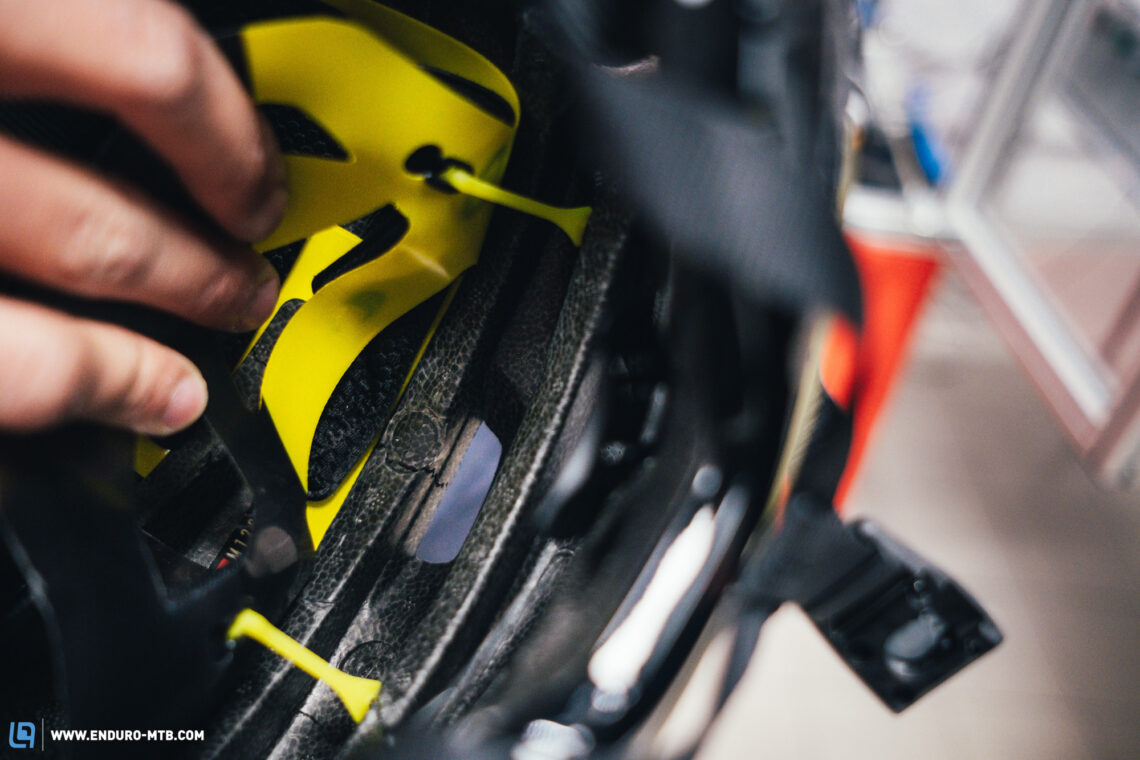
Koroyd sits between the EPS shell and your head
Koroyd is a system made up of countless tiny tubes that are welded together, forming a kind of honeycomb structure, placed between the EPS shell and the wearer’s head. The tubes crumple upon impact and thereby promise to absorb direct as well as rotational forces. You’ll predominantly find the system in helmets from SMITH and ENDURA.
Fox Fluid Inside
The renowned protective gear brand Fox rely on pads filled with oil that promise to absorb both right angled impacts and rotational forces. This is thanks to the high viscosity of the oil inside the pads.
POC Spin
The POC Spin system is very similar to MIPS technology, relying on floating pads that mitigate rotational forces acting on the helmet.
Leatt Turbine
The Leatt Turbine system is made up of rubber rings attached to the inside of the helmet. They’re somewhat reminiscent of turbines and significantly denser than standard pads which should allow them to absorb head-on impacts. Thanks to the fins attaching the outer to the inner ring, the pads can also deform horizontally and thereby absorb rotational forces.
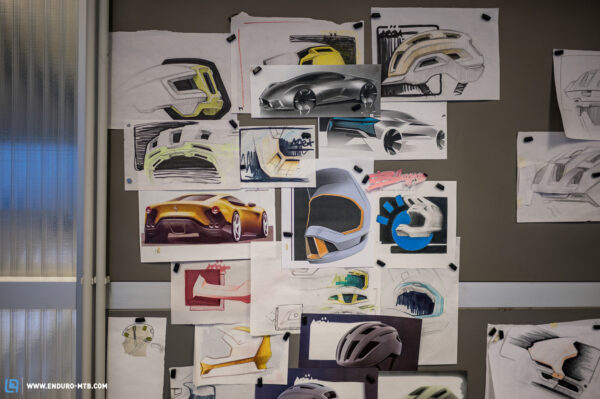
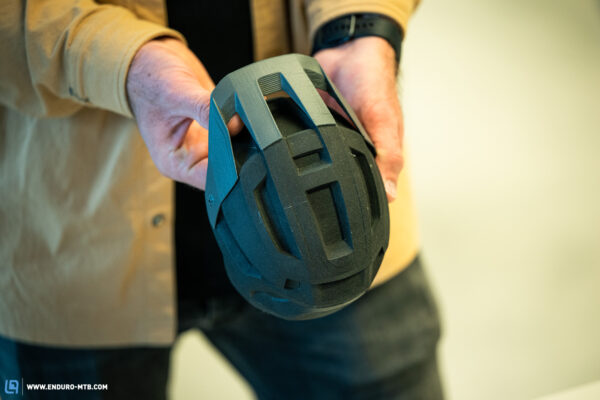
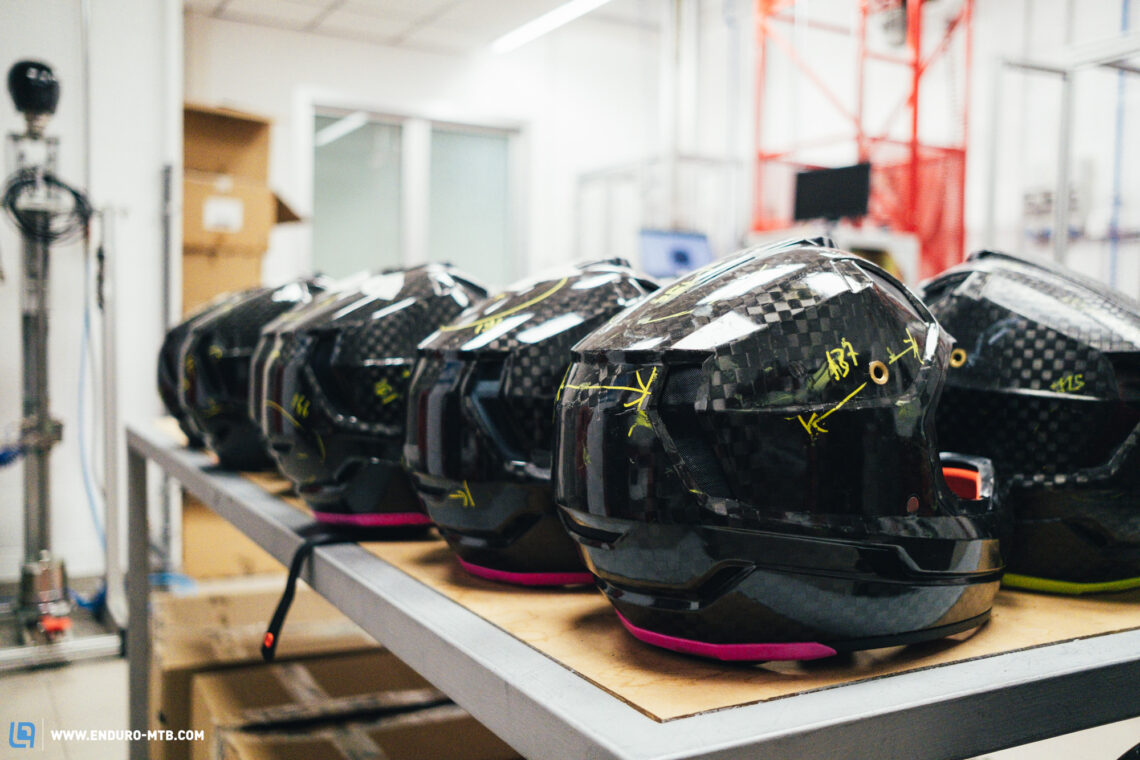
Back and knee pads and the secret material
Knee, elbow, and other protectors rely on the same protection principle as helmets, which is to absorb impacts. While helmets rely on relatively hard EPS foam, back and knee pads are usually made of a soft, often viscoelastic foam, offering the best possible wearing comfort. The preformed pads are usually embedded in a robust material, over which some manufacturers put a hard plastic shell to prevent the pad from snagging on anything when you crash, sliding over the ground instead. Besides the black foam, which is typically supplied by SAS-Tec, you’ll also find knee pads that rely on the distinct orange foam from D3O.
How does D3O foam work?
D3O isn’t R2D2’s small brother from Star Wars, but rather a new kind of foam that seems to be both soft and hard at the same time. At room temperature, when you’re wearing it on your body, the foam is soft and flexible, guaranteeing optimal comfort. When you crash and fall on the pad, the foam’s structure changes and hardens instantly. The above-mentioned MET Bluegrass Seamless back protector relies on D3O foam. In this example, the foam follows a beehive structure to offer improved ventilation.
What is Rheon polymer?
Rheon polymer has similar traits as D3O foam, allowing it to harden upon impact while remaining soft at room temperature. Additionally, Rheon have developed an algorithm that lets the foam mimic an optimised hive structure and arrangement, taking their inspiration from nature. The resulting structure isn’t uniform, but rather features the most efficient and protective arrangement, according to Rheon. Among others, Rapha use this foam in their trail knee pads, which came out on top in our big ENDURO knee pad group test.
How do back and knee protectors get tested?
There are no testing standards or certifications for protective gear for cyclists, which is why most manufacturers rely on the EN 1621–1:2012 standard used to certify motorcyclists’ limb joint impact protectors. To comply with this standard, a 5 kg metal weight gets dropped onto the protector from about 1 m. The protector sits on a spherical anvil that contains sensors to measure the force transferred through the pad. Without any pads, the force is about 180 kN, which corresponds to about 18 tons. With a protector, the maximum force is not allowed to exceed 35 kN, spread over 9 measuring points. For the higher level 2 protection class, the maximum permissible force drops to 20 kN. These protection levels provide a good orientation when shopping for knee pads.
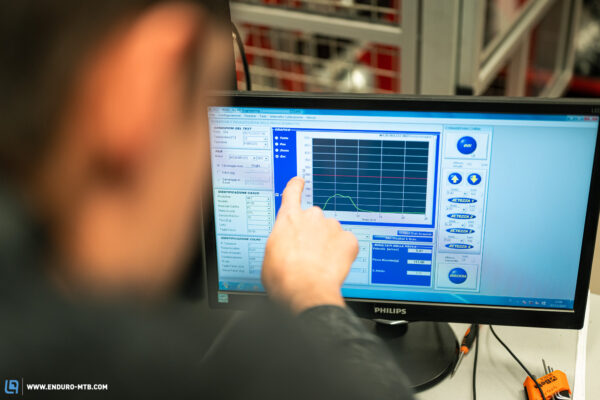
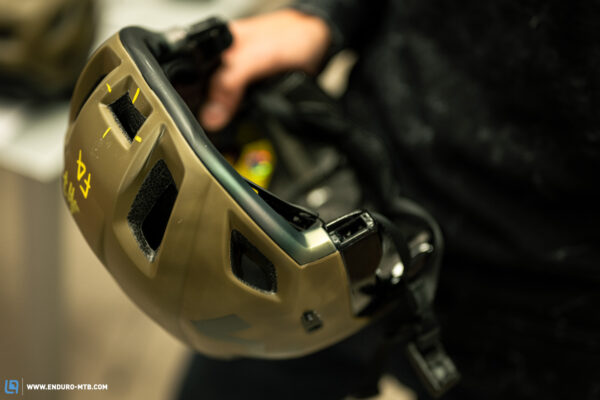
A lid for every pot
When it comes to protecting the different parts of your body in case you lose control of your bike, the same applies to these as to your head. The technology behind modern protective gear is fascinating, functional, and expensive. But even the best safety equipment doesn’t free you from the responsibility of not overstepping your boundaries and pushing your luck. As you progress, you will experience setbacks, and your body will have to take the occasional hit – as with so many things in life, it’s a matter of trial and error. With a modern helmet and the right protective gear, however, you can at least do so without sweating bullets every time you ride or ending up having to drink food through a straw at 50 years old, and you can look stylish, too.
Our summary on buying protective gear
The helmets that you find at your local bike shop will all comply with the minimum safety standard that applies in your country. It’s different online, where you’ll be able to purchase completely uncertified protective gear, so be careful when shopping from home. It’s up to you to decide whether you want something with additional safety features like SPIN, Koroyd, Turbine, or MIPS, the effectiveness of which isn’t certified by standardised testing procedures. Therefore, the system you trust depends solely on your own judgement.
Thanks to the high-tech protection systems found in modern pads, you can tailor the amount of protection you want to your own trail riding requirements. Open- or full-face, light- or heavy-duty knee pads, with or without a back pad. If you’re familiar with the trails, know what to expect and you can judge your own riding skills realistically, you’ll be able to make certain compromises, though within a reasonable limit.
You should never go riding without taking any protective measures, the minimum requirement being a helmet. Moreover, we recommend taking a look at when your pads were manufactured. If they’re very old, you might want to buy yourself a new set and profit from the latest technological advancements.
Better safe than sorry – Our conclusion
Protective kit isn’t cheap, but it’s come a long way. So, it’s worth keeping up to speed: the status quo isn’t as good as it will ever get. Besides that, we’re all shaped differently, so keep on looking until you find something that fits your body and your riding style. Also, try upgrading your old kit: you’ll be amazed at how much you’ll like wearing your new lightweight protectors and how good you look in them. Ultimately, the best protectors are useless if you don’t wear them.