[Interview] Renthal’s R&D Engineer Simon Brocklehurst
A month back during our visit to Renthal we spoke Simon Brocklehurst senior research and development engineer for bicycle parts. Renthal as we looked at previously has some of the most advanced component production facilities in the world and has taken the market by the horns and showed riders what type of quality products can be made for mountain bikes. Their products turn up in all kinds of places including on pro riders bikes that have no sponsorship agreements with Renthal. Knowing how they think and arrive at what they make is always interesting.
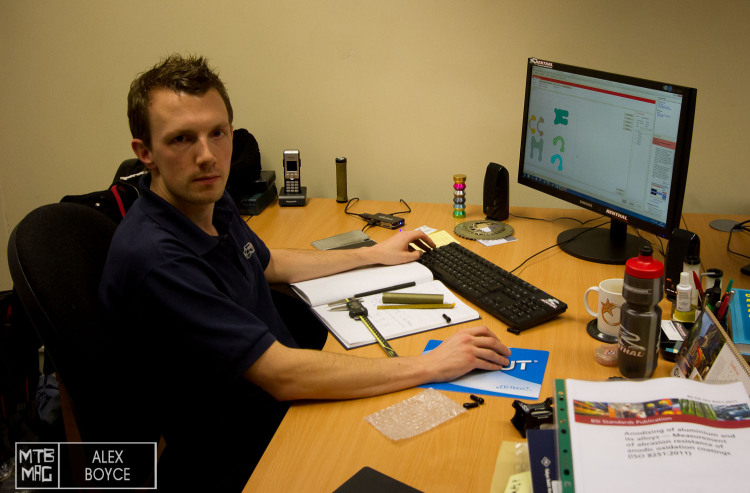
What do you exactly do at Renthal?
I work on new product development, overseeing design and manufacturing of products I’m also responsible for all the new parts post the Duo stem, for examples the Apex Stems and we are working on a whole range of products about to be released, we also work on some motorcycle products. Some of the time it’s me doing the design work, other times im testing products or overseeing whats going on.
I’m heavily involved in the bespoke testing programs that I developed and I ride as well.
When you go for a ride does it influence what you are about to design?
There are always things that you like to design for yourself, that aren’t always suitable for mass market, but when discuss a new product it is also about a personal take not just what the market might want.
To design a good mountain bike product you need to be able to mountain bike and have some idea what makes a good in use product. Actually riding a bike and having a bit of a feel for a jump and what actually goes into the product gives a better idea of what is going on with your part you are designing.
What were the ideas behind the Duo stem?
It was a balance behind structural performance and stiffness and strength.
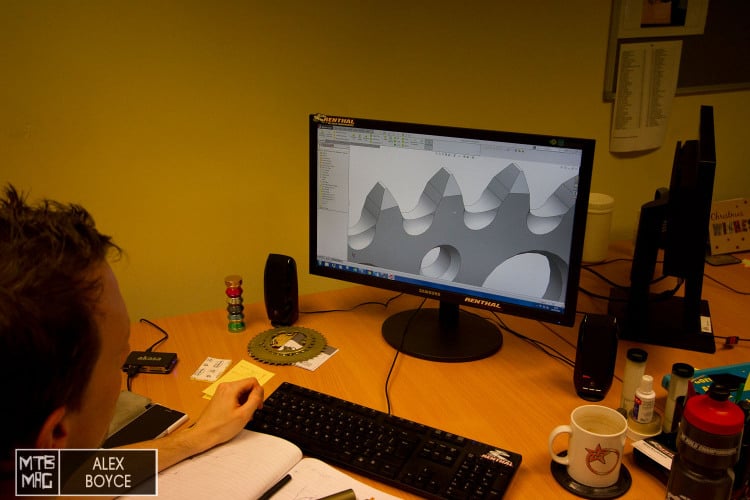
How do you know what your baseline is?
We look at what else is on the market, but we also do a lot of data acquisition work, going riding and looking at real world forces that go through the products. A lot of products on the market are over engineered for what they need to be. We can save weight, as some products have been based on laboratry conditions then a safety factor added in on top.
How much responsibility do you have of the safety aspect of designing a part?
All of it really, we have to design to the EN standard, then strain gauge tests to determine how far above EN we have to go.
How do you design a bar?
First you need to know what geometry you are going to design to, back sweep, width and upsweep, then looking at it from a commercial point of view, what you want bars to look like, then deciding what stiffness you want and how you want it to feel.
Where is the golden rule about that?
We do comparative testing, we do rider testing with those products and try and correlate what a rider like with regards to feeling, relative to the data. Art and science mixing together. With the carbon bars though we did blind testing so it was not possible to tell whose bar was whose. There were conclusive results that most riders preferred one bar although they couldn’t see what they were riding. That was our lite bar at the time. We look at all elements of the construction of a bar then tune it to see what feel we want to give it.
What are you working on now? How do you predict what to make next?
To some extent it’s a commercial driven thing rather than an R and D thing, all that feeds from the commercial side. We then try to produce it.
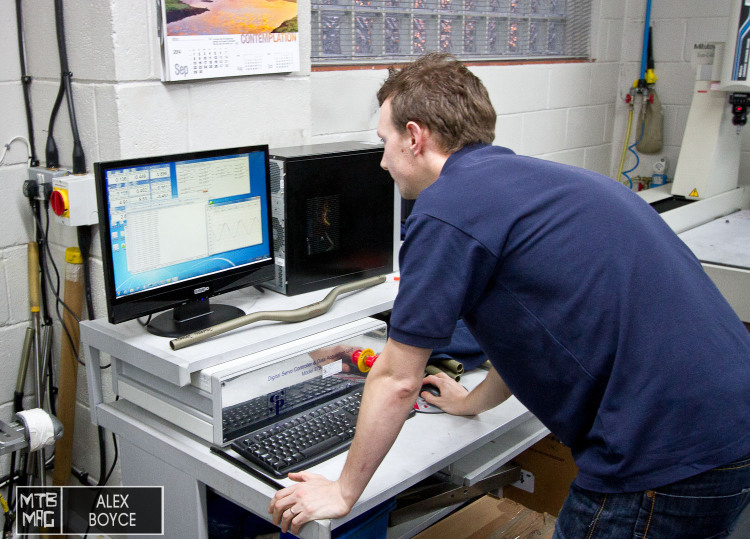
Any mad professors trying stuff then?
No, not really, it would cost a lot of money and take a lot of time and not necessarily make a commercially successful product. We also need a return on it. We only make stuff people want and is accepted by the market. We can’t make to a really small subset of riders.
Any ideas you have had which wouldn’t work?
Yes quite a few, where we discovered the machining costs and production costs would not make a commercially successful product.
Do you have to design new machines to make your products?
Yes, in the fatigue testing lab we made a new machine to test with, we have bought in new machines for CNC work to make sure we can handle the volumes and complexity of design.
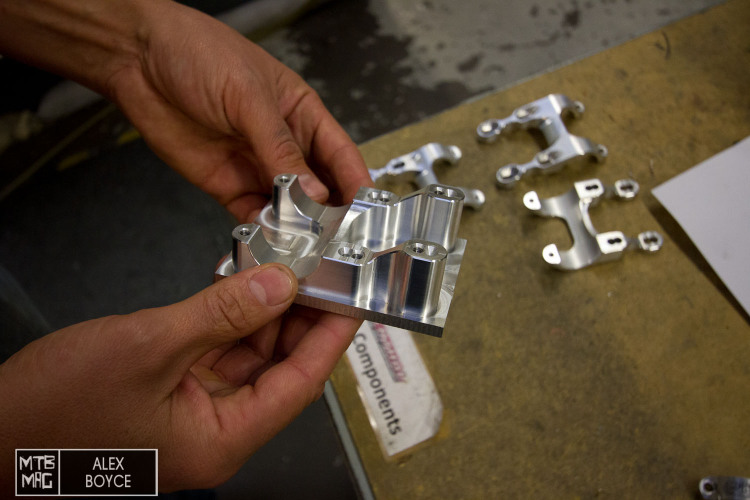
Is everyone else in the market chasing your heels?
In certain products we are highly regarded, there are other products where other people have been established longer and therefore are selling more and are better known.
Do you dream about stems and bars at night?
Ha ha, try not to… all of us who are into bikes can’t help thinking about stuff all the time, especially as an engineer.
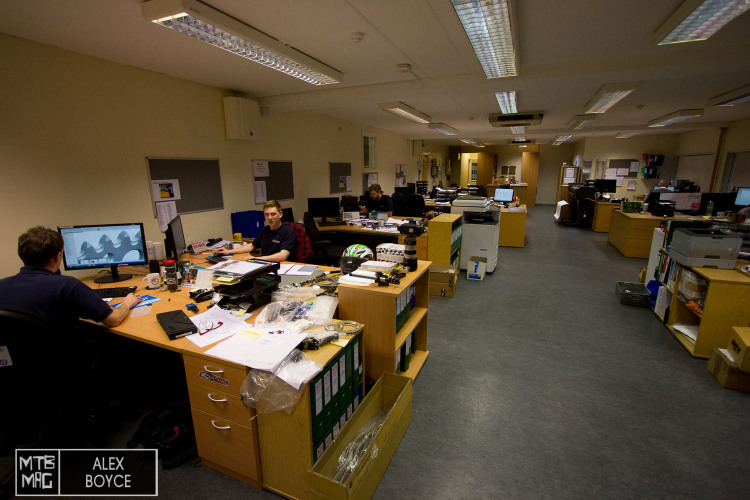
Is this your dream job?
There are always bits you don’t like, but as an engineer who likes mountain biking, it’s pretty good.
How do you feel when you are riding a bike with your stem or bar on it?
Quite proud, to have a product on it but more proud when you see other people with it. At Fort William last year Renthal Fat bars and stems where everywhere and that makes you feel quite good.
How do you choose your artistic style when designing things?
My background has been structural, you look at different ways of doing things and are influenced by so many things including cost of making it what the market likes, so many different things there are a lot of external parameters that influence it.
Which feature are you proud of the most of one product you have made, and have you influenced the market?
I think for our Fatbar lite carbon, what it offers for weight and feel to ride, thats one I’m proud of, and also the new one…. how it performs compared to competitors. Can’t say what it is! Coming soon. People have been influenced by what we have done, and it’s better for mountain bikers that companies do their own different things.
The post [Interview] Renthal’s R&D Engineer Simon Brocklehurst appeared first on MTB-MAG.COM.